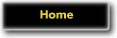
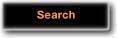
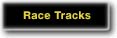
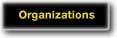
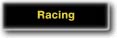
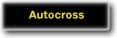
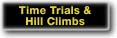
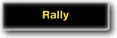
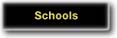
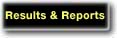
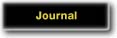
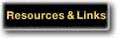
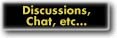
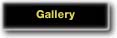
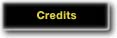
These notes were recently sent out by Bob Corbitt, National Administrator of Scrutineering
The screws that secure the throttle plate on these cars are normally split on the bottom of the throttle shaft . At the Runoffs® two years ago a competitor brought it to our attention that in one of the sections of the rules for these classes, there is a statement that non-standard fasteners may be used in all but certain specified areas. The competitor removed the split tail on the throttle shaft screw. We did not believe that this is a violation of the carburetor rule.
Air dams: when checking to determine if the air dam is not any lower than the rim, remember to check on the lowest point of the rim. Most of these cars have a lot of negative camber and need to be checked on the inside of the rim.
Rear brake ducts through the rear bulkhead behind the driver in a production car were found to be not in compliance by the SOM.
Intake manifold: Per tech at the Runoffs® in 1995 and 1996, we have allowed the bottom of the intake manifold (as seen through the carburetor opening) to be profiled (grooved) with any configuration. An agreement between tech and the major engine builders present approved the filling of the water passages with plastic (Devcon, etc.). When grinding the intake manifold bottom, the engine builders agreed not to expose more than a quarter (U.S. 25 cent piece) of the epoxy filling. This is normally seen at the #2 cylinder runner in the manifold.
Several of the top finishing T1 cars were disqualified for cylinder head modifications. A careful inspection of the cylinder head is necessary to determine if material has been removed from the Chevrolet aluminum cylinder head. The best way to verify this is with a sample head from a dealer. The narrowing of the divider between the intake ports is one indication that is easy to see. A tool may be fabricated from a piece of stiff wire in the shape of a U with pointed ends to measure from the face of the head to the floor of the intake port to demonstrate how much material has been removed. Also check the short turn radius of the port for removal of material and smoothing.
The heads that we looked at seemed to have been bead blasted to restore the rough surface. A close comparison with a part of the head that still has the original sand casting will show you the difference.
The removal of any material in the head, ports, manifold is not permitted.
If there is sufficient interest in track and rim bars Bruce Turner may make another production run. He will need 8 to 10 confirmed orders (with deposit) before he will consider making them. Estimated cost for track bar is $ 250.00 plus freight. The track bars are 1 inch aluminum tube with laser engraved 0.1 inch scales on both sides. These track bars can be configured to measure inside to outside or outside to outside. The bar breaks down into two 45 inch pieces. Contact Bruce Turner at 4861 Farber Row, Columbus, Ohio, (614) 771-1560.
FV: Never attempt to check either the under tray or body work since we have totally lost the ability to define flat. Signed: The Target